Operational Efficiency Boost for a Specialty Food Manufacturer
Project overview
THE CLIENT
A specialty food manufacturer known for its artisanal, small-batch gourmet sauces and condiments. The company had built a strong reputation in boutique grocery stores, specialty food retailers, and direct-to-consumer (DTC) sales. Despite growing demand, the company faced operational inefficiencies that were causing production bottlenecks, increasing costs, and straining supplier relationships.
THE CHALLENGE
The brand was experiencing delays in production, high operational costs, and inconsistent inventory levels, which impacted both wholesale and DTC order fulfillment. Their supply chain was disorganized, with fluctuating lead times and inefficiencies in raw material procurement. Additionally, the company lacked a streamlined data tracking and reporting system, making it difficult to forecast demand accurately and control costs. The business needed a structured approach to improve efficiency, reduce costs, and scale production without unnecessary financial strain.
OUR ROLE
We performed a full operational audit to assess inefficiencies in supply chain management, production workflows, and inventory control. Our goal was to streamline operations, reduce waste, and improve cash flow management so that the company could scale more efficiently without increasing overhead costs.
We got to work
With our Fractional CFO and Business Consulting expertise, we:
- Analyzed the supply chain to identify bottlenecks and inconsistencies in raw material procurement and lead times.
- Negotiated better supplier contracts, securing improved pricing and more reliable delivery schedules.
- Streamlined procurement processes, implementing a demand-based ordering system to reduce excess inventory by 30%.
- Implemented lean manufacturing principles to improve efficiency on the production floor, reducing waste and optimizing labor use.
- Introduced new inventory management tools to provide real-time tracking of raw materials and finished goods, improving forecasting accuracy.
- Redesigned production workflows to minimize downtime between batches, increasing overall output by 40%.
- Enhanced warehouse organization and fulfillment processes, reducing order processing times and improving on-time delivery rates.
- Developed a financial roadmap to align operational decisions with long-term profitability goals.
- Created KPI tracking dashboards to monitor efficiency, labor productivity, and cost savings in real-time.
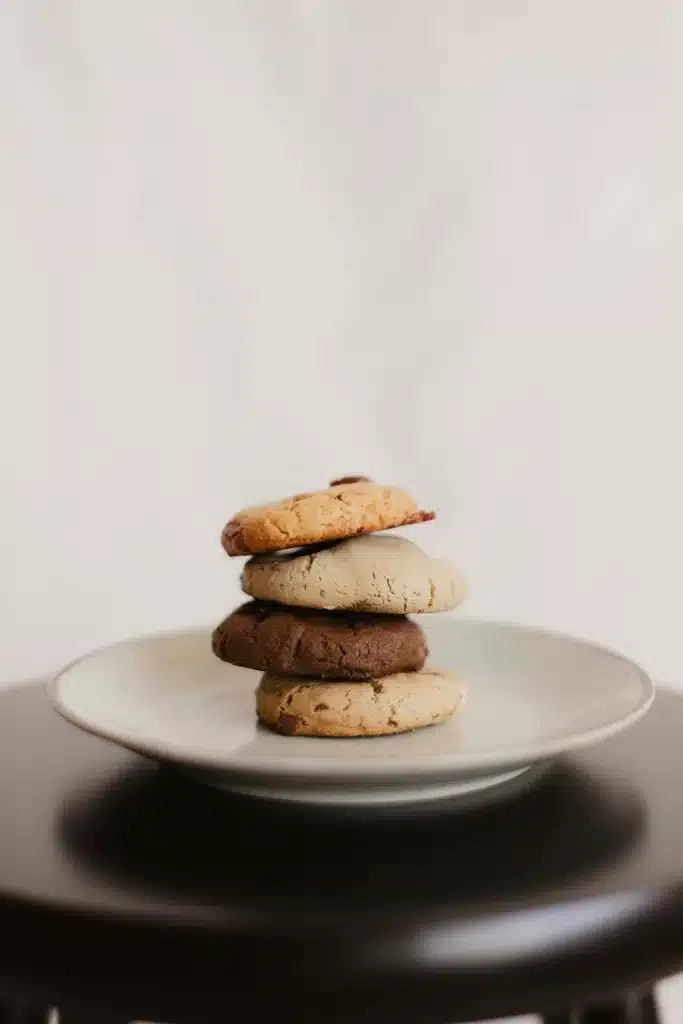
Results
By streamlining supply chain operations, improving production workflows, and optimizing inventory management, this specialty food manufacturer significantly reduced costs and increased production capacity. With a more efficient and scalable operational structure, the company is now better positioned to meet growing demand while maintaining profitability and cash flow stability.
Increased production output by 40% without additional labor costs.
Reduced order processing times by 25%, improving wholesale and DTC fulfillment.
Increased production output by 40% without additional labor costs.